Construction Phase Support
Gas Protection Measures Validation
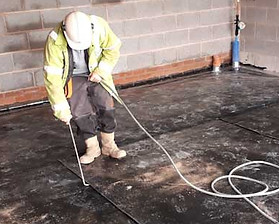
Where ground gas risk assessment recommends that gas protection measures should be installed into new properties, it is now a requirement of BS8485 that the installation be validated by an independent appropriately qualified engineer.
The validation requirements should be clearly set out in a Gas Protection Measures Implementation and Validation plan. which takes account of the ground gas regime (often defined as a Characteristic Situation) and the foundation and floor slab details. Validation often takes the form of visual inspections of the sub-floor void and its ventilation together with integrity testing of the lapped and sealed joints which is usually conducted by air-lance testing.
Specialist IDG staff can attend site to validate the installation of measures and conduct integrity testing.
More information on our ground gas validation services can be found here.
Cover Soils Validation
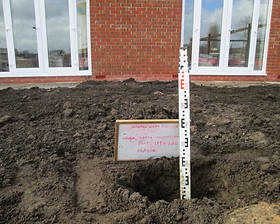
Where low concentrations of contaminants are present in either natural or Made Ground soils on a development site, a common remediation technique is to isolate these soils below a layer of clean natural sub-soil or topsoil to break the direct contact contaminant linkage.
Cover soil validation is the independent verification that cover soils are suitable for the proposed use, free from contamination and of sufficient thickness as detailed in the remediation strategy.
Cover soil validation is usually undertaken on completion of the construction phase and is often the final remediation requirement prior to occupation of the property. A CSV report is required by the local planning authority to discharge planning conditions and by the developers warranty provider (LABC or NHBC) prior to sale of the property.
Stockpile Characterisation and Assessment

Independent sampling and chemical testing of excavated soils is required to assess subsoil and topsoil for its suitability for use in clean cover layers, or to classify stockpiles of waste soils for retention on site or disposal off site.
Where waste soils are to be exported to landfill, materials need to be fully chemically tested to satisfy duty of care requirements and to classify the material as inert, non-hazardous and hazardous waste. In addition inert or non-hazardous waste required waste acceptance criteria testing (WAC testing) for it to be accepted by the receiving landfill.
Increasingly, materials management plans (MMPs) in accordance with the CL:AIRE DoWCoP require detaield characterisation of materials movements on site and as direct transfers of clean naturally occurring materials between sites.
We can attend site to sample and arrange independent chemical testing of stockpiled soils on your behalf. Please contact us for details.
Materials Management Plans and QP Services

Soils (Made Ground or natural deposits) are considered to be waste at the point of excavation. If these “waste” soils are placed back into the ground or transferred to other sites, it could be deemed that waste has been disposed of without a permit. The person disposing of the waste and anyone who knowingly facilitates the disposal may be liable for payment of Landfill Tax. All parties involved could also be liable to penalties for non-compliance and face criminal prosecution.
A Materials Management Plan (MMP) can be produced in accordance with the CL:AIRE Definition of Waste, Construction Industry Code of Practice (DoWCoP) which will provide details of the source and contaminative state, excavation, stockpiling, placement or disposal of soils to provide evidence of the intended purpose of excavated materials to avoid the possibility of the materials becoming subject to either waste management legislation by the Environment Agency or landfill tax by HM Revenue and Customs (HMRC).
A Qualified Person (QP) is required to sign a declaration confirming that the MMP has been prepared in accordance with the DoWCoP.